Products List
- Silica brick for glass kiln...
- BG-98 superior silica bricks for gla...
- Insulating silica brick...
- High thermal shock resistance and ze...
- High bulk density and High thermal c...
- Unshaped refractory Silica Refractor...
- Silica brick for hot blast stove...
- Silica brick for coke oven...
- Silicon brick for carbon furnace...
Classic Case
-
British Refractories customers to
June 7, 2011 the British Refractories Company custo...
-
Turkish customers to visit our fa
On 26 July,2013 Turkey customers visited our fact...
Refractory Knowledge
Zero Expansion Silica Brick for Hot Repair of Glass Furnaces
Date:2015-11-06 14:20 From:Zhengzhou Sunrise Refractory Author:admin
In the middle and late period of glass furnaces, fire holes may appear in the crown of the melting zone and regenerator and the upper part of the collapsed partition wall. If the holes are too big, the operation and production may be threated.
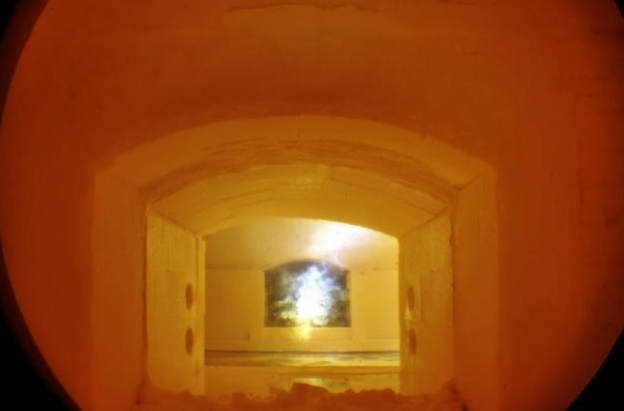
If fire holes appear in those parts, the traditional repair method is hot repair mix plugging after cooling the water cooler. The drawback of this method is that water may spill under the 1590℃ high temperature corrosive gases. In addition, with the increase of fire holes, more water coolers are added which will increase the fuel consumption.
Suitable refractories are used to replace water coolers. Those refractories for hot repair should have the following the features:
1) Excellent thermal stability. When performing the hot repair, the refractories will be directly put into the 1600℃ environment. So, it must have good thermal stability and no peeling or burst.
2) Good chemical stability, excellent corrosion resistance to alkali and no pollution to glass.
3) Sufficient mechanical strength, good strength at room temperature and high temperature, can be cut and drilled.
4) Excellent high temperature performance, stable volume at high temperature, no huge expansion or contraction, high softening temperature under load.
5) Reasonable price, low once-investment and high cost-efficiency.
Refractories used for the hot repair of glass furnaces include zircon brick, mullite brick, fused cast AZS block, silica brick and chrome or silica hot repair mixes.
Due to the harsh environment in the glass furnace, zircon brick or mullite brick may burst or spall when used for hot repair. This may pollute the glass liquid. In addition, Fused cast AZS and zircon brick are expensive and too heavy and difficult to be machined into desired sizes and shapes.
Silica brick is cheap, but common silica brick has bad thermal stability and big thermal expansion and may crack during use. It cannot be directly used for hot repair and requires pre-heating before use. it cannot be tightly integrated with the crown, which increases the risk of further corrosion by alkali gases. Hot repair with common silica brick is difficult and takes a long time, and the result is poor.
Zero expansion silica brick can meet all the requirements above. It is made of high-grade quartz ore. High-grade quartz ore is made into fuse silica by melting, cooling, crushing, screening and pickling. Then fused silica is mixed with mineralizing agent and sintering agent to form semi-dry mud. Then the semi-dry mud is processed into bricks by pressing, drying and sintering. Its main mineral composition is amorphous fused silica. Since its thermal expansion coefficient is very low, close to zero, it is called zero expansion silica brick.
Zero expansion silica brick has high purity, 99% SiO2 and 0.3% impurities. It has no risk of iron contamination during long-term use. It has good thermal stability and excellent corrosion resistance to alkali.
Different from other materials, its flexural strength increases with the rising of temperature. Zero expansion silica brick has a high softening temperature under load, up to 1680 ℃. And it can be made into special desired shapes.
With zero expansion silica brick and micro-expansion hot repair mixes, fire holes can be repaired without the shutdown of the furnace. It is time-saving and can effectively expand the service life of furnaces.
Contact Us
- E-mail :sales@sunriserefr.com
- Phone : +86-371-63838939
- Fax:+86-371-63835539
- Company Address : No.36 Fengchan Road Of Zhengzhou, Henan, China (Mainland)